CAR T-therapy can treat advanced cases of blood cancer, but an ongoing challenge is logistics. The work turning a patient’s own immune cells into a cell therapy happens in a distant lab. Transportation to and from that site plus manufacturing time puts the wait for treatment at a month or more. Galapagos aims to shorten the timeline and improve patient access with technology that manufactures the therapy at the hospital where a patient is receiving care.
During the annual meeting of the American Society of Hematology in San Diego earlier this month, Belgium-based Galapagos reported early-stage clinical data showing its technology was able to produce CAR T-therapies in seven days. Furthermore, those therapies led to treatment responses with a safety profile in line with currently available cell therapies.
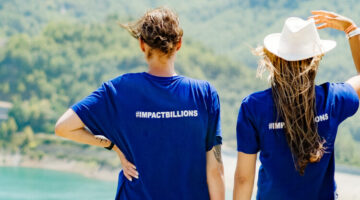
The Impact Brands: Empowering Wellness Through Natural and Holistic Solutions
In an era of escalating healthcare costs and a growing preference for natural, holistic approaches to health, The Impact Brands emerges as a collective of diverse brands dedicated to supporting overall wellness through natural means.
These studies are small and more testing is needed, but Galapagos contends the preliminary results show point-of-care manufacturing can work. One key limitation of currently available CAR T-therapy is that the long manufacturing time means it’s unable to address fast-progressing cancers, said Jeevan Shetty, the company’s head of clinical development oncology.
“We’re not putting patients on a list in hopes of getting treatment, but [instead] treating patients close to their homes and addressing rapidly progressing disease,” he said, speaking to journalists in a presentation during the ASH conference.
The technology that enables manufacturing at a clinical site is a cell therapy manufacturing platform called Cocoon. This enclosed system turns a patient’s cells into a personalized cell therapy in a device about the size of a microwave oven. Cells are placed in the fully automated system. A technician presses a button. One week later, the manufacturing process is complete. A clean room can house multiple Cocoons to make cell therapies for many cancer patients.
Galapagos presented data for two cell therapy candidates it produced with Cocoon. GLPG5201, a potential treatment for relapsed or refractory chronic lymphocytic leukemia, has preliminary results from a dose-finding Phase 1 study. As of a Sept. 6 cutoff date, 13 of 14 patients who could be evaluated for efficacy showed an objective response to the therapy; eight of 14 patients achieved a complete response. At the higher dose level, all eight patients showed a response to the treatment and five of eight achieved a complete response.

At ViVE 2024, Panelists Share Prior Authorization Progress and Frustration in Payer Insights Program
At the Payer Insights sessions on Day 1 of ViVE 2024, a panel on prior authorization offered compelling insights from speakers who shared the positive developments in this area after years of mounting frustration. Speakers also shared challenges as they work with providers to figure out how policy developments and technology will work in practice.
[Paragraph updated to add Phase 1 data.] The second Galapagos CAR T-program is GLPG5101, which is in development for relapsed or refractory non-Hodgkin lymphoma. In the Phase 1 portion of the study, 12 of 14 patients (86%) showed an objective response; 11 of those 14 (79%) achieved a complete response. In the Phase 2 portion of the study, as of the Sept. 1 cutoff date, six of the seven evaluable patients showed a response to the treatment; a complete response was observed in four of the seven.
The main safety concerns for CAR T-therapies are an immune response called cytokine release syndrome and neurotoxicity. Both were observed in the clinical trials, but Sebastian Anguille, head of hematology at the University of Antwerp and an investigator in the studies, said these adverse effects were manageable. He said the key factor is the faster turnaround time for the cell therapy which can get a patient treatment before the disease rapidly progresses.
Galapagos, which was founded in 1999, initially focused on developing small molecule drugs primarily for inflammatory conditions. Cancer drug research represents what Shetty describes as “a new era for Galapagos.” The company gained access to Cocoon last year through its €125 million (about $138.4 million) acquisition of CellPoint, a cell therapy developer partnered with the technology’s maker, the contract manufacturing giant Lonza. CellPoint brought to the table a proprietary software system that enables remote monitoring of the manufacturing process in real-time.
By bringing cell therapy production to a clinical site, a hospital becomes a manufacturing location that falls under some regulatory oversight. In Europe, each location is a GMP facility that is certified by local authorities, said Ruiz Astigarraga, Galapagos’s head of manufacturing. He expects a similar approach will be adopted in the U.S. Astigarraga added that Galapagos audits these sites to ensure they comply with standards.
Galapagos is not the only company trying to make cell therapy manufacturing faster and more efficient. Cell Shuttle, the enclosed and automated manufacturing system of Cellares, can make cell therapies in about one week. Cellares is not developing its own cell therapies, but the startup has research partnerships with companies that are testing Cell Shuttle with their experimental therapies. The technology of Gracell Biotechnologies offers next-day cell therapies. That speed proved attractive to AstraZeneca, which this week agreed to acquire the China-based company for $1 billion up front.
Meanwhile, Galapagos is pressing forward with a third cell therapy manufactured with the Cocoon technology. Last week, the company began a Phase 1/2 study with GLPG5301, an experimental CAR T-therapy for advanced cases of multiple myeloma.
Photo: Yuriko Nakao/Getty Images